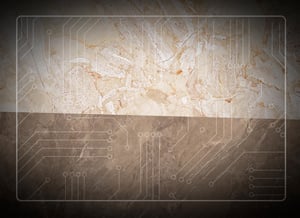
Input systems
Our input systems are tailored to your specific needs.
Our input systems at a glance
Our customers opt for input systems/HMIs that stand out from well-known mass-produced products. Our input systems are customer-specific, made from high-quality materials and designed and engineered down to the last detail.
One outstanding example of our innovative strength is our Agnostic Touch technology. This is based on highly sensitive force sensors that detect even the finest mechanical bends. Our product range also includes DYNASENSE technology, a unique membrane keypad that has been specially developed for harsh outdoor conditions.
By combining innovative technologies and high-quality materials, we create input systems that are not only functionally impressive, but also meet the highest aesthetic demands. Our customized solutions are the result of many years of experience and a deep understanding of the individual needs of our customers.
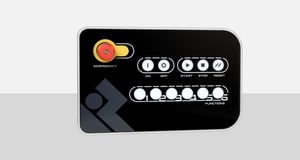
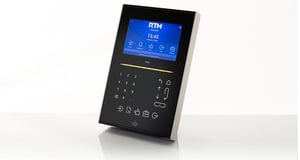
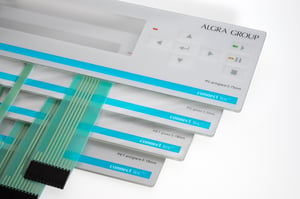
With DYNASENSE, any plastic surface is child's play to operate. Attractively priced, robust and suitable for all weather conditions.
Find out more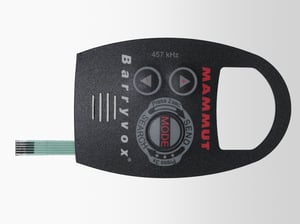
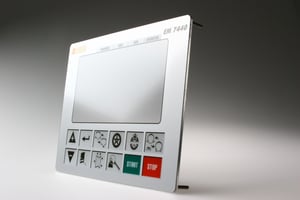
Piezo technology also works behind aluminum surfaces. With DYNAPIC and DYNASIM, there are two classics of this technology to choose from.
Find out more"Our customized input systems combine innovative technology, high-quality materials and sophisticated design to create a unique solution that perfectly combines functionality and aesthetics."
Our input systems in comparison
Comparison of typical input solutions
Our solutions are individually tailored to your requirements.
Get in touch with us
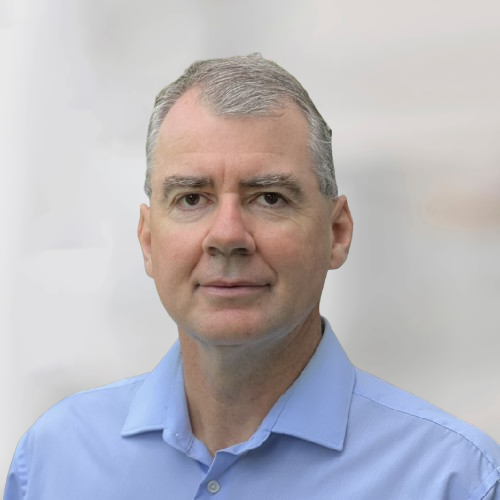
SCHNEIDER Franz
Sales Manager Human Maschine Interfaces
f.schneider@algragroup.ch
Mobile: +41 79 513 89 40