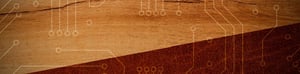
Modern input systems at a glance
Operating devices is the norm for us.
Modern input systems: How we control
our devices
The cell phone is with us day and night. It reacts to information that we enter in one way or another. The technology for touch operation on smartphones is called PCAP or Projected Capacitive Touch. All devices with which we communicate require modern input systems. On a notebook, we normally use a keyboard and a mouse. Ticket machines, for example, use buttons, often in conjunction with a screen. Dishwashers, ovens, mixers - all these appliances have buttons. In cars, we also use buttons, touch screens, rotary wheels, joysticks, voice commands and sometimes gestures - an expressive movement with which we transmit a command. Depending on the input and requirements, different technologies are selectedas the HMI (Human Machine Interface) or input system.
Different types of pressure sensors for input systems
There is a type of sensor behind every button. It detects whether a button is pressed. This activates a consumer or the information of the button press is passed on to a control device. The typical, simple switch, for example a light switch, closes or interrupts the circuit. Light on: Circuit is closed. Light off: Circuit is interrupted. The circuit is therefore closed or interrupted by a mechanical movement. Most buttons are based on the on-off principle.
Typically, input systems are implemented as follows:
- Normally open contacts
- Resistive sensors
- Piezoelectric sensors
- Capacitive sensors
- Agnostic sensors
Computer keyboards, copier keys, keys on various household appliances, etc. usually have short-stroke keys or microswitches. On membrane keyboards, contacts are closed by a metal dome. Most buttons have such "closing contacts". The advantages: simple signal evaluation, natural tactile feedback through a key stroke, no power consumption in idle state. The disadvantages, on the other hand, are: a mechanical opening around the button, existing dirt edges, the input panel is not waterproof and has a limited service life. In the case of membrane keyboards, there is also the fact that the requirement for a plastic film as the operating front restricts the design options. Both variants are susceptible to vandalism.
How a resistive touchscreen works...
Resistive touch, such as a resistive touchscreen, works as follows: The front film is pressed onto the back film and makes a contact. In this case, the electrical conductors are almost invisible so that the screen behind the resistive touch remains visible. Such a keypad consists of conductive tracks, which are often designed as a matrix. The movable foils as a surface are a condition and limit design variants. If the front foil is defective, the input system usually no longer works. The resistive touchscreen has now been largely replaced by capacitive touch or PCAP.
When a capacitive sensor makes sense...
A capacitive sensor works completely differently: it is a type of sensor that uses changes in the capacitance of an electrical capacitor to detect information about the environment or react to touch. The capacitive sensor contains electronics that detect the change in capacitance and convert it into an electrical signal.
In order for a change in capacitance to be detected by the approach or touch of a finger, the input front must be non-conductive. Glass or plastic as an input front fulfills this condition. However, all metallic surfaces are unsuitable. If the triggering finger is electrically insulated, for example by wearing gloves, no change in capacitance can be detected. No signal is triggered. This also applies when the device is operated using a pen or a key. If the capacitive operating surface is wet or dirty, the resulting capacitance change is filtered out using complex algorithms. The challenge here is to distinguish an intended key press from other disturbances. We realize this when the intended function fails to occur or is triggered with a delay (for example, on a ceramic stove). However, depending on the humidity, the use of hand cream or the degree of soiling, capacitive technology is susceptible. The press of a button is not recognized or is only recognized after repeated operation.
In principle, a capacitive sensor can also be used as a pressure sensor. The operating surface is displaced or deformed by a button press, which changes the plate distance and thus the electrically measurable capacitance. This also works with metallic fronts. However, process-reliable signal evaluation is not easy to achieve, as the capacitance is also influenced by heat.
A piezoelectric pressure sensor works
via electronic evaluation
The piezoelectric pressure sensor also falls under the list of common input systems: a metallic membrane is coated with piezoelectric material and firmly connected to an operating front. When the button is pressed, the piezo disk is slightly stretched. This causes it to emit a voltage that can be evaluated electrically. The electronic evaluation of voltage is more complex than, for example, a change in resistance. It can be difficult to distinguish between a "heat signal" with rapid temperature changes and a button press. This technology is less suitable for a long keystroke.
What is meant by
strain gages?
The most common pressure sensors are based on strain gauges. For example, weight measurements for scales. Strain gauges detect changes in electrical resistance caused by the stretching or deformation of a material.
The Agnostic Touch technology as a new solution
among the input systems
Agnostic Touch technology makes use of strain gauge technology. The small, highly sensitive force sensor with integrated Wheatstone bridge circuit is soldered onto a circuit board using SMT assembly. The circuit board is in turn glued to the back of the operating front. Pressing the button then triggers a mechanical bend, which is transmitted by the sensor as a change in electrical resistance. There is normally one sensor per button. Depending on the geometry or application of the input, different arrangements make sense. This is because the greater the force applied, the greater the mechanical deformation of the operating surface. The electrical resistance changes linearly to the deformation. The force of the keystroke therefore serves as an additional input dimension.
What makes the Agnostic Sensor so
special?
There are no limits to the material of the operating surface. Only a minimal mechanical bend in the micrometer range is required on the operating surface. With a 1 mm thick stainless steel front, a force of a few 100 grams is sufficient - similar to a touch on a smartphone. This is almost unimaginable and very impressive to experience.
In addition to metallic surfaces such as stainless steel or aluminum, glass, ceramic or a wooden front panel are also suitable for agnostic input. It can also be operated using a finger, a pen, a key or a tool. Regardless of whether the environment is wet, cold, hot or dirty. This makes this technology an ideal solution for a wide range of machines, devices and appliances.
With Agnostic Touch technology, the signals from all sensors on the input front are evaluated by software. Force exerted on the surface is reliably registered. This results in stable and clearly assigned key signals. Pressure in the area between the keys or undefined bending of the surface is reliably filtered out thanks to our pattern matching algorithm. After calibrating the input system with a defined force, the desired trigger force can be set individually.
Get in touch with us
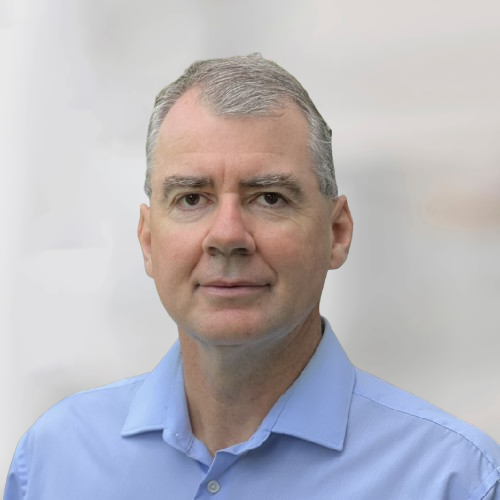
SCHNEIDER Franz
Sales Manager Human Maschine Interfaces
f.schneider@algragroup.ch
Mobile: +41 79 513 89 40